Filtre Toz Keki Yeniden Çökelmesi
Jet Pulse Torbalı Filtrelerde Temizlememe Sorunu ve Çözümü
Jet pulse temizleme sistemi verimliği, toplanan tozu hazneye düşürmekten daha önemli olan aerosol parçacıklarının yüzeylere sabitlendiği bir süreçtir (redeposition). Pilot ölçekli bir jet pulse filtrede yeniden çökelme miktarını ölçmek için toz izleme teknikleri kullandık. Deney sonuçlarına dayanan matematiksel bir model ile, torbadan torbaya toz transferini, torbalardaki yeniden çökelmeyi ve toz haznesine taşıma işlemini tanımlamak için geliştirdik. Filtre torbalarının üzerine toz reddi çökmesi artan filtreleme hızı ile belirgin bir şekilde artarken, filtre torbalarına bitişik torbalara göç ve yeniden çökelme artmıştır. Mümkün olan en düşük basınç düşüşüyle çalışmak için yüksek hızdaki jet pulse filtreleri için filtre keki yeniden çökelmesi en aza indirilmelidir.
Jet pulse filtre torbaları, diğer yöntemlerle temizlenen filtrelerden daha yüksek yüzeysel filtrasyon hızlarında çalıştığı için son yıllarda yaygın olarak kullanılmaktadır. Filtrenin gerekli yüksekliği ve ilk maliyeti hız arttıkça azaldığından filtreleme hızını daha da arttırmak cazip gelmektedir. Amaç, basınç düşüşünü düşük tutarak, toplama verimliliğini korurken de torba ömrünü uzun tutup filtrasyon hızını arttırmaktır. Sonraki yazımızda, partiküllerin bir jet pulse filtreye nüfuz etme mekanizmasını inceleyeceğiz. Bu yazıda, yüksek filtreleme hızı ve filtre keki yeniden çökmesi arasındaki ilişki tartışacağız. Makul basınç düşmesi korunacaksa, yüksek hızda artan yeniden çökeltme sorunu en aza indirilmelidir.
Filtreleme hızına karşı basınç düşüşü çizimi olan Şekil 1, basınç düşüşünün filtreleme hızı ile hızla arttığını, bunun da ötesinde, kullanılan basınç düşüşü dikkate alınmadan hızın arttırılamayacağı bir sınır değerine ulaştığını düşündürmektedir. Şekil 2, bu çalışmada elde edilen verilerden alınan filtrasyon hızına karşı bir basınç düşüşünün bir grafiğidir. Bu veriler için, darbeler arasında beslenen toz miktarı, hız arttıkça filtreleri orantılı olarak daha sık titreşerek sabit tutuldu. Basınç düşüşünün hızla arttığı tespit edildi. Darbeli jet filtreleri, yüksek filtrasyon hızlarında çalışacak şekilde adapte edilmeden önce aşırı basınç düşüşüne neden olan bu faktörleri tanımlamak ve aşmak gerekir.
İsimlendirme
Denklemi ile tanımlanan Ci matrisi. 5
Denklemi ile tanımlanan C2 matrisi. 9
Denklemi ile tanımlanan C3 matrisi. 10
H (t) zaman t – 1 ve zaman t arasında hazneye düşen renk etiketli toz
Filtre torbası üzerine yeniden koyan bir temizleme darbesiyle temizlenen toz fraksiyonu
İki komşu torbanın her birinde (3 torbalı bir ünitenin) yeniden tazelenen bir temizleme darbesi ile serbest bırakılan toz K2 fraksiyonu,
Hazneye düşen bir temizleme darbesiyle boşaltılan K3 toz fraksiyonu
Mi (t) t zamanında torbadaki renk etiketli toz kütlesi
M (t) sütun vektörü, t zamanındaki her torbadaki toz miktarını tanımlar
Temizleme sırasında, filtre keki yaklaşık 100 mikron çapında toz tortuları olarak bir jet pulse temizlenmiş kefeden ayrıldığını belirtti. İdeal olarak, aglomere edilen filtre keki toz toplama hunisine topluca düşürmektir. Bunun yerine, kekin bir kısmı geldiği torbanın üzerine veya komşu torbalar tekrar yapışabilir. Filtre kekinin yeniden çökmesi gerçekleştiği ölçüde, jet pulse temizleme etkisiz olacaktır. Jet pulse temizleme sırasında üretilen toz bulutunun sinefotografik gözlemleri, toz aglomeralarının kumaş yüzeyinden 200 cm / s’lik bir başlangıç hızı ile uçurulmuş bir gazda 10 cm’ye kadar çıkması için yeterli üfleme yaptığını göstermektedir.
Gaz Filtre gövdesi içinde sessiz olmadığı için, aglomeraların yansıtılacağı mesafe torbalar arasındaki mesafeyle karşılaştırılabilir. 100 mikronluk bir katı parçacık, yaklaşık 50 cm / s’lik bir terminal yerleşim hızına sahiptir ve bu nedenle, 244 cm boyunda standart bir torbanın üstünde veya ortasında bir noktadan toz toplama hunisine düşmesi birkaç saniye alacaktır. Düşük yoğunluklu bir toz aglomera, hazneye düşmesi daha uzun sürebilir. Bu süre zarfında, bazı aglomeraların yeniden toplayacağını ummak mantıklı görünüyor.
Not: Aglomera tanelerden oluşan bir karışımın bağlayıcı madde ile birleştirilmesinden meydana gelen yapı öğesi. Kaynak )
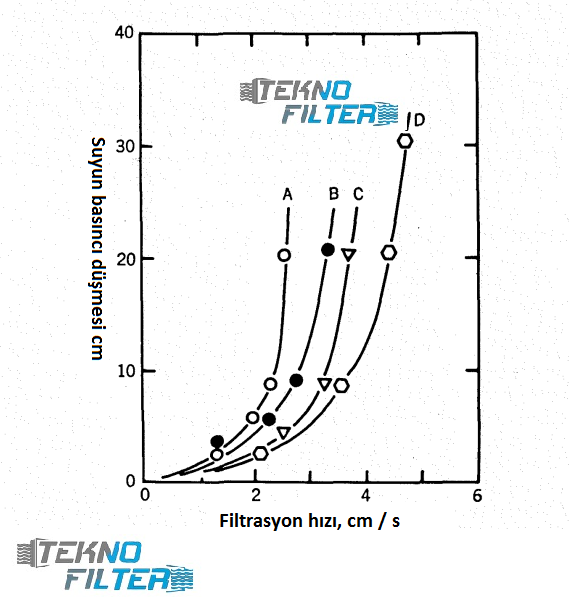
Şekil 1. 325 gr yün keçesi için B1’den gelen basınç düşüşü / filtrasyon hızı, 23 gr / m3’de talk tozu. (A) huni girişi, 1,9 cm basınçlı hava valfi, 100 ms “açık” süre, 1 dak. Devir süresi; (B) aynı üst giriş; (C) aynı 2.54 cm basınçlı hava valfı; (D) aynı, 38 ms “açık”, 1: 43 dak. Çevrim süresi.
Filtrasyon hızı arttıkça daha fazla yeniden çökelme meydana gelebilir, çünkü yüksek filtreleme hızı toz kek yığınlarını torbaya doğru sürüklemeye yardımcı olur. Bazı torbalı filtrelerde kaba parçacıkların doğrudan toz haznesine düşmesine izin vermek için filtre mahfazasının tabanının yakınında gaz girişleri bulunur ve bunlar için dökme gaz akışı yönü yukarıya doğrudur. Filtre hızı arttıkça filtre torbaları birbirinden uzaklaşmadıkça, muhafaza içerisinde yukarı doğru gaz hızı artar ve yeniden çökelme için toz agregalarını tutma eğilimi gösterir. Yeniden çökme meydana geldiğinde, filtre torbalarındaki toz birikiminin kalınlığı artar ve basınç düşmesi yükselir. Hız arttıkça, yeniden çökeltinin toplamı ve filtre kekinin hiçbirinin hazneye düşemeyeceği bir noktaya ulaşılabilir. Bu gerçekleştiğinde, basınç düşüşü stabilize olmaz, sabit filtrasyon hızı limitsiz bir şekilde yükselir.

Şekil 2. Mevcut deneylerdeki basınç düşüşü vs. filtrasyon hızı.
Ekipmanlar
Bu çalışmada kullanılan jet pulse filtre, sırayla sıralanmış üç polyester iğnelenmiş keçe torbasına sahipti; Her torba çapı 11.4 cm ve boyu 244 cm idi. Torbalar piyasada iyi bilinen bir imalatçı tarafından imal edildi ve 1.3 cm’lik su basınç düşüşünde 15 cm2 / s’lik bir geçirgenliğe sahipti ve yüzey işlemi yoktu. Torba kesit alanının gövde kesit alanına oranı, torbaların genellikle daha yakından durduğu endüstriyel ünitelerde bulunandan daha küçük bir oran olan 1 ila 5 idi. Gaz, gövde üstünden 24 cm aşağıda merkez hattı olan 20 cm çaplı bir kanaldan girildi.
Dikeyden 40 derecelik eğimli duvarlara sahip piramit bir huni toplanan tozu almıştır. Filtre muhafazasının önü, 0.64 cm kalınlığındaki emniyet camı, 0.95 cm kalınlığında şeffaf akrilik plastik ile kaplanmış ve filtrasyon ve temizleme işlemlerinin gözlemlenmesine izin vermiştir. Şekil 3, jet pulse filtrenin bir çizimidir. Şekil 4’te gösterilen boyut dağılımı ile uçucu kül bir kömür yakma programı kazanından elektrostatik olarak çökeltildi ve tüm deneyler için bir test tozu olarak kullanıldı.
Uçucu kül sistemin hava girişine sürekli olarak bir yıldız toz besleyicisi ve pnömatik aspiratör vasıtasıyla beslendi. Merdiven diskindeki basınç düşüşü, gazın hacimsel akış hızını ölçmek için kullanıldı. Filtreden temizlenen gaz, bir akış regülâtöründen, bir radyal fanı, akustik susturucudan ve bir atık hava sistemine geçti. Deneysel yöntem, etiketlenmiş bir test tozuna ve etiketsiz bir toza ihtiyaç duydu. Uçucu kül suda çözünmesi, uçucu kül eklenmesi ve boyayla ağırlıkça % 0.5 etiketli bir toz. Etiketli tozun boyut dağılımı da Şekil 4’te gösterilmektedir. Etiketli toz, bir yıldız toz besleyicisi 6 ile aerosol haline getirilmiş ve üstten 60 cm merkez torbanın etrafından geçen kapalı bir halka şeklinde oluşturulan 0.6, 4 cm boruya beslenmiştir. Halka, radyal konumlarda, etiketlenmiş uçucu külün halka içerisindeki merkez torbanın üzerindeki banda doğru akmasına izin vermek için deliklere sahipti. Yıldız toz besleyici, üç torbaya etiketsiz uçucu kül besleyen pnömatik blower bağımsız olarak açılıp kapatılabilir.
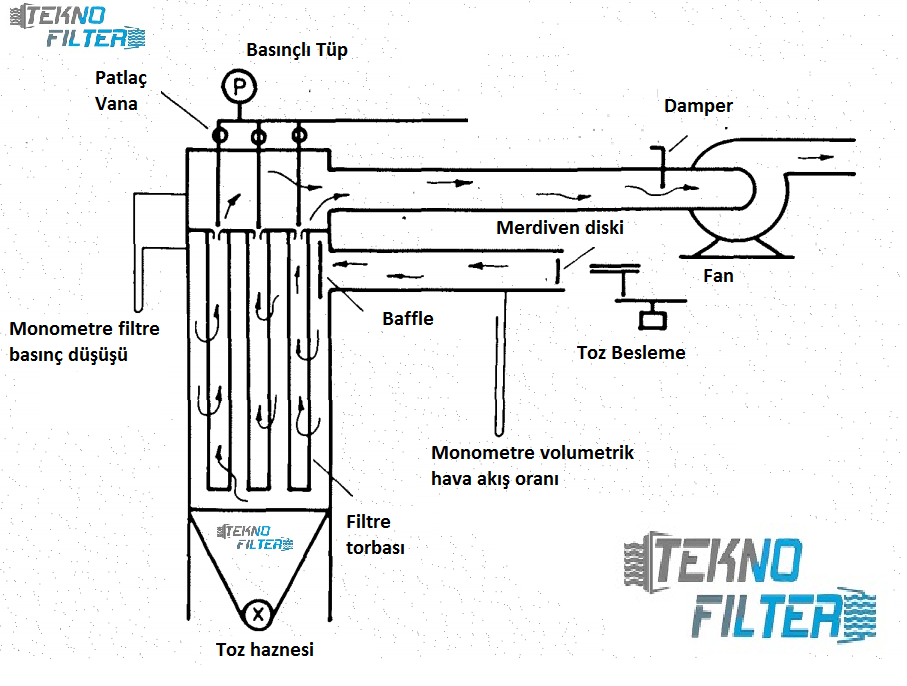
Şekil 3. Torbalı filtre pilot ünitesinin şematik gösterimi
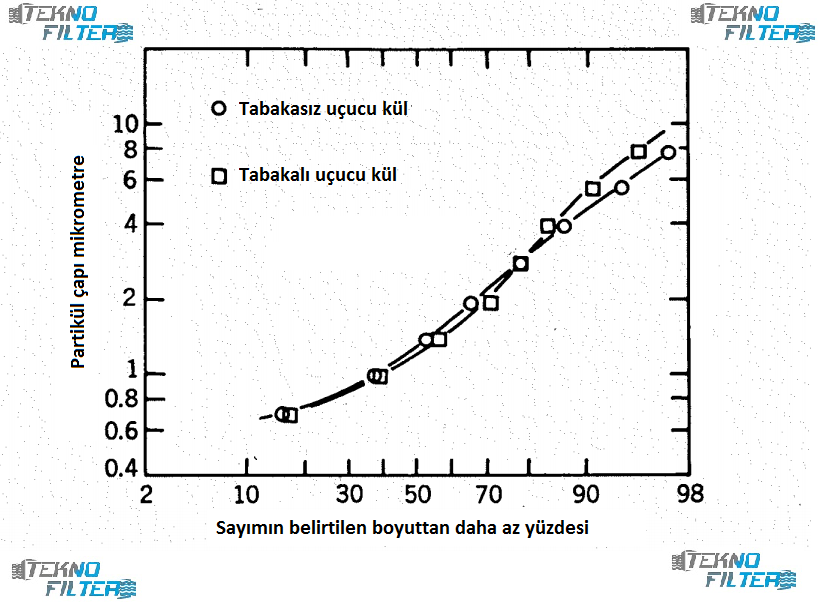
Şekil 4. Sayımla, etiketsiz ve etiketlenmiş uçucu külden kümülatif boyut dağılımları.
İşlem
Deneyler filtre torbaları boyunca 5,10 ve 15 cm / s’lik yüzeysel filtrasyon hızlarında gerçekleştirildi. Her bir deney için, sistem, sabit filtrasyon hızı ile çalışırken basınç düşürme dengesine getirildi ve uçucu kül, sabit bir hızda giriş hava akışına beslendi. Orta torba, uranine etiketlenmiş uçucu kül ile merkez torbanın darbeleri arasında bir dakika süreyle bu tozu halka boyunca besleyerek şartlandırıldı. Bu arada ve her deneyin geri kalanında, c torbanın hepsinde toplanması için giriş gaz akışına etiketsiz uçucu kül beslendi. Temizlik tamponuyla bir torbadan kurtulmuş toz, o sırada torbadaki tozu temsil eder. Hazne içine düşen serbest toz her bir temizleme darbesinin ardından değiştirilen bir plastik şişe içerisinde toplandı. Bu yolla, her torba üzerindeki toz numuneleri, etiketlenmiş toz verildiği anda elde edildi. (Uranine: Oftalmolojide bir tanı aracı olarak kullanılan, kimyasal adı Floresein sodyum tuzu, ticari adı uranine olan bileşik)
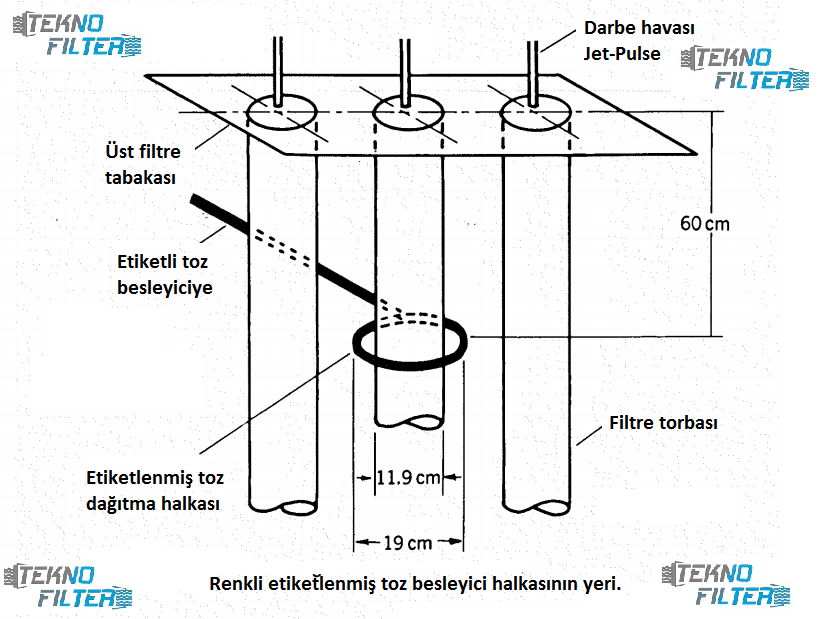
Şekil 5. Renk etiketli toz besleme halkasının yeri.
Her palsın ardından hazneye düşen toz içindeki uranine konsantrasyonunu izleyerek, uçucu külün komşu torbalar ve hazneye ne derece geçtiğini matematiksel bir model kullanarak belirledi. Temizleme esnasında iyi şartlandırılmış bir torbadan kurtulmuş olan tozun, kumaş yapısında kalan tozdan etkilenmediği düşünülmektedir. 3 haznede toplanan toz numuneleri, 15 ml su ile karıştırılarak uranin analizi, asılı tozu çıkarmak için santrifüj yöntemiyle analiz edildi Kül ve bir Fotovolt çoğaltıcı Flüoresan Ünitesi ile flüoresans ölçümü. Dikkatle, bu tekniği kullanarak 10 ~ 10 g / ml kadar düşük uranin konsantrasyonları ölçülebilir. Tüm deneyler için atım basıncı 7 atmosferde (103 psig) sabitlenmiş, atım frekansı dakikada torba başına bir darbe Ve patlaç valfi elektrikli olarak 75 milisaniye idi.
Tartışma
Yüksek filtreleme hızının jet pulse filtre performansı üzerindeki etkisi daha net hale getirilmiştir. 5 cm / s gibi klasik bir filtreleme hızında bile, bir temizleme darbesiyle torbadan çıkarılan tozun çoğunun toz haznesine düşmektense yeniden çökeldiğini göstermektedir. Bu nedenle, yeniden çökeltinin asgariye indirilmesi, filtrenin geleneksel hızlarda kullanılması durumunda bile önemlidir. Filtrasyon hızı arttıkça, yeniden çökelme arttı. Filtre torbada yeniden tortulanan serbest tozun fraksiyonu, filtreleme hızı 5 ila 15 cm / s arasında arttıkça 0.38’den 0.83’e yükseldi. Aynı zamanda, tüm komşu torbalarda yeniden tortulanan toz fraksiyonu 0,50’dan 0,16’ya düştü. Torbaların yeterince temizlenmesi açısından daha önemli olan, filtrasyon hızı 5 ila 15 cm / s arasında arttığı için toplam fraksiyonel yeniden çökeltinin 0.88’den 0.99’a yükselmesi. Toz haznesine düşen fraksiyon (bir kez redepoze edilen fraksiyon), 0.12’den 0.01’e düştü. Hızın artması torbaların daha az etkili şekilde temizlenmesine yol açtı.
Şekil 6. Renkli etiketlenmiş toz uygulandıktan sonra puls sayısı ile Uranin konsantrasyon oranı. Hız, 15 cm / s.
Geleneksel hızlarda, toz kek aglomeraları temizleme darbesi sırasında kirli gaz akışının içine uzatılabilir. Bununla birlikte, yüksek filtreleme hızlarında, aglomeralar filtre torbasının yüzeyinden uzaklaşmakta güçlük çekebilir, çünkü filtreleme gazının yüksek hızı tozu tekrar torbaya süpürme eğilimindedir. Filtrasyon hızı arttıkça, yeniden çökelme öncelikle komşu torbalardan ziyade filtre torbasının üzerine yapıldı. Yeniden yığılma arttıkça, filtre keki daha kalınlaştı; toz kekinin daha küçük bir kısmı hazneye düştü ve basınç düşmesi arttı. Yeterince yüksek filtrasyon hızında, yeniden çökelme olabilir ve buda tozu düşürmez. Bu noktada, toz keki kalınlığı artmaya devam edecek ve sabit filtreleme hızı artık korunamayacağına kadar basınç düşüşü sınır olmadan artacaktır. Bu, yeniden çökelmenin, Şekil 1 ve 2’de gösterilen filtrasyon hızı ile basınç düşüşünde olağanüstü hızlı artıştan sorumlu olduğunu düşündürmektedir.
Burada açıklanan sonuçlar kullanılan deney düzeneği bağlamında alınmalıdır. Her ne kadar ticari jet pulse filtre bileşenleri kullanılmış olsa da, üç torba pilot birimi ticari bir birimden daha küçüktü ve biraz farklı geometriye sahipti. Üç torba birer birer püskürtüldü, her seferinde toplam torbanın % 33’üne püskürtüldü. Çoğu torbaya sahip büyük endüstriyel birimler, daha düşük bir orana sahiptir; sadece bir defada torbaların % 5 ile % 20’sini temizler. Sonuç olarak, üç torbalı deney ünitesindeki her püskürmemiş torba, temizleme sırasında darbeler arasındaki süre boyunca işleyecekleri % 50 daha fazla havayı tutmak zorunda kaldı.
Bir endüstriyel ünite için her filtre torbası sadece % 5 -% 25 daha fazla havayı işler. Bu nedenle, deneylerimizde komşu torbalara toz göçü abartılmış olabilir. Deneysel filtrenin minimum torba torba mesafesi yaklaşık 12 cm iken endüstriyel bir jet pulse filtresi içindeki torbalar daha fazla olabilir. Torbalar birbirine yakın olduğunda komşu torbalar göç etmesi gerektiği için, deneylerimiz tam ölçekli bir filtreden oluşan komşu torbalara göç miktarını hafife almış olabilir.
Deneysel filtrede yüksek atımlı torba oranının ve daha büyük torba aralığının net etkisi bilinmemektedir. Bununla birlikte, deneysel filtrede artan torba aralığından kaynaklanan, darbeli torbaların artan bir fraksiyonundan kaynaklanan komşu torbalar üzerinde daha fazla yeniden çökelme ve komşu torbalar üzerinde yeniden çökeltinin azalması bir miktar dengelenmelidir. Deneysel filtrenin sadece üç torbası olduğu için, endüstriyel bir filtrede olduğu gibi, kumaşın çoğu, ilave torba yüzeyi yerine konut duvarlarına bakmakta. Duvarlar, komşu bir torbaya veya toz haznesine göç etmesine izin vermek yerine tozları filtre torbasına geri yansıtabilir. Bu nedenle, bu deneyler kendi kendini yeniden tortulaşmayı aşırı tahmin edebilir. Dikkatli bir tasarımla en aza indirgenmiş olsalar da ölçeklerin pilot tesis deneylerindeki ölçeğin etkileri hiçbir zaman tamamen ortadan kaldırılamaz.
Jet Pulse Torbalı Filtrelerde Temizlememe Sorunu ve Çözümü nde Teknofilter olarak buna ek olarak, bir pulse-jet filtresi performansı burada tartışılanlardan daha fazla parametreye bağlıdır. Parçacık boyutu, kumaş malzeme yapısı, nem, sıcaklık dahil gaz özellikleri, torba uzunluğu, aralığı, diğer değişkenler gibi toz özellikleri ve yeniden çökeltme filtre davranışını etkileyebilir. Pulse basıncı, torba ivmesini etkiler çünkü darbe basıncı, süresi ve form yeniden yoğunlaşma ve temizleme etkinliği üzerinde güçlü bir etkiye sahip olmalıdır, bu da toz kek yığınlarının torba yüzeyinden yol alacağı mesafeyi etkiler. Artırılmış torba aralığı, komşu torbalar üzerinde yeniden çökelmeyi önlemeye yardımcı olurken kısa torbalar da, filtre torbasının üzerine yeniden çökme olanağını azaltmalıdır. Temizleme darbesinin boyut ve biçimindeki değişiklikler, torbanın temizlenebilirliği ve yüksek hızda yeniden yığılma üzerinde önemli bir etkiye sahip olabilir.
Filtre mahfazasına, torba uzunluğuna ve aralığına ve temizleme darbesinin niteliğine göre değişiklik, yeniden çökeltiyi azaltmak için etkili olmaktadır. Buna ek olarak, bazı torbalar belirli uygulamalar için diğerlerine kıyasla avantaj sağlayabilir. Her pulse-jet uygulaması için en etkili torbanın tanımlanması yapı ve operasyonel değişikliklerin faydalarını çoğaltır.
Özet
Bu çalışma, bir jet pulse torbalı filtresindeki filtre kek yeniden çökeltisinin derecesini belirlemiş ve basınç kaybı etkisini tartışmıştır. Geleneksel filtreleme hızlarında, bir temizleme darbesinden kurtulmuş tozların çoğu, filtre torbasına komşu torbalar üzerine yeniden koyulur. Daha yüksek filtrasyon hızlarında, yeniden çökelme daha belirginleşir ve yeniden çökme için en önemli alan darbeli torbanın kendisiydi. Yüksek hızda torbalı filtrelerin daha uygun hale gelmesi için filtre keki yeniden çökeltisinin kontrol edilmesi gerekir. Burada bildirilen testler, şu anda endüstride kullanılanların tipik filtre yapım ve temizleme prosedürlerini yansıtıyor. Filtre keki yeniden çökelme problemini en aza indirmek için yenilikçi değişiklikler gereklidir. Bunlar, bu araştırma programının bir sonraki aşamasında araştırılacaktır.
Jet Pulse Torbalı Filtrelerde Temizlememe Sorunu ve Çözümü konusunda uzmanlarımıza danışmak için web sitemizi ziyaret edebilir bilgi alabilirsiniz.